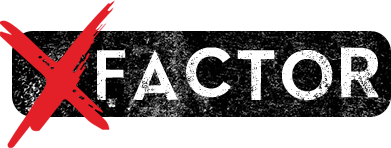
Men of Steel
A superlative show seals Afcons a place in history for reincarnating the iconic Mahatma Gandhi Setu
“I assure you that this iconic bridge will not only be important in the history of Bihar, but also of the country as well.” These words from Shri Nitin Gadkari, Union Minister of Road Transport and Highways, during the inauguration of the eastern flank of Mahatma Gandhi Setu, were an approval of a colossal achievement in Indian engineering. The Gandhi Setu after its reincarnation has taken its place as the longest steel bridge (5.6km approx) of the country.
For the first time in India, an entire superstructure of a balanced cantilever bridge was replaced with a simply supported steel superstructure. Almost 67,000MT of steel was used in its construction. Few Indian urban bridge projects in recent memory have witnessed such huge steel consumption. It’s not just the quantity of steel, but its fabrication across the country, and subsequently its transportation to the bridge location which gave it epic proportions.
“The procurement of steel was a huge challenge considering it included high performance steel. All the steel was procured domestically and transported to different parts of the country for fabrication to ensure speedy work. We had to consistently engage various modes of freight even during the pandemic so that the fabrication and movement to site was unaffected. At times, we even had to shift materials from one fabricator to another to maintain work continuity. It’s not for nothing that such a large quantity was successfully procured, with about 30,000MT procured in a single year during the peak period,” says Project Manager SK Misra.
The fabricated steel structures arrived at site after dismantling activities were completed for the upstream lane. To expedite execution of downstream side, the team begun planning of parallel dismantling and erection by the end of upstream lane completion. The planning was prioritised for the intermittent and wet spans which resulted in completion of downstream side in less than 18 months.
“The execution of the downstream side was significantly impacted by two cyclones — Tauktae and Yaas — and the deadly second wave of Covid-19 pandemic. However, our pre-planned approach of parallel working not only helped in timely completion of all 11 intermittent spans, but also completing the entire erection activities in just 13 months,” Misra says.
“For completing 11 intermittent spans, we had a limited window of only six months in dry season. It included 24,000MT of concrete dismantling, 3,000 cum of pier cap concreting and 7,500 MT of erection. The parallel work approach was such that as soon as the dismantling was completed, the pier cap team and the erection team took over simultaneously. While the pier cap team was handing over the spans to erection team for truss launching, the erection team completed the intermediate portion staging & truss erection of the span, excluding the pier cap portion. This needed meticulous planning and monitoring, and it’s safe to say that we did it successfully,” he adds.
Our work methods were such that dismantling had minimum impact on the environment. The use of high reach boom jaw cutter along with dust suppression system to dismantle dry spans was efficient and cost-effective too. And in wet spans, we used wire saw cutting method with gantry arrangement for upstream and holding frame arrangement for downstream side. We did not let any debris fall in the Ganga River, and I see that as a tremendous success.
- S K Misra, Project Manager
But all this is not as easy as it seems. And if you bring in the factor of extreme weather conditions, the situation changes dramatically, quite literally.
“We worked in a region where temperatures vary from over 42oC in summers to less than 10oC in winters. In summers, we face sandstorms, and the strong hot winds affect concreting and erection activities. Also, the low draft in the river complicates manoeuvring of marine vessels. In monsoons, the river swells to over twice its size with very high river currents. Flooding is also common. And winters, along with low temperatures, bring extremely low visibility due to fog,” Misra explains.
The entire Gandhi Setu team performed like a well-oiled machine. Learnings from constructing the upstream side prepared them for future hurdles. The team acted intuitively, made advance preparations, and responded to the challenges wisely.
“Our work methods were such that dismantling had minimum impact on the environment. The use of high reach boom jaw cutter along with dust suppression system to dismantle dry spans was efficient and cost-effective too. And in wet spans, we used wire saw cutting method with gantry arrangement for upstream and holding frame arrangement for downstream side. We did not let any debris fall in the Ganga River, and I see that as a tremendous success,” Misra explains.
Because of a highly-motivated team and its superlative performance, Afcons will hold a place in history for successfully reincarnating the iconic Mahatma Gandhi Setu.


